General construction of compounding extruder package
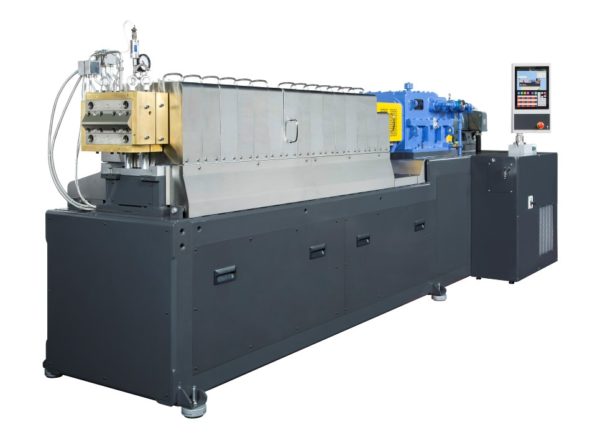
The TEX34αIII model replaces the slightly smaller TEX30α small-lot extruder and, as with other TEX-series extruders, its screw diameter is 36 mm. The extruder’s exceptionally high torque density (18.2 Nm/cm3) enables effective yet gentle compounding at low screw speed and optimally low temperature, but without detriment to throughput.
See details (PDF)
1. Degassing
De-gassing cylinder "DGC" effectively remove and exhaust gas out of low bulk density plastics naturally or by force. Bulk density of feed material is remarkably increased with DGC, and therefore, processing rate can be significantly increased due to improved feeding ability.
Here, we introduce our new developed "De-Gassing Cylinder — DGC" on our twin screw extruder TEX, which helps you to solve feed-neck problem as above and significantly increase processing rate in plastics compounding with low bulk density material.
See details (PDF)
Recently, demands on high throughput – high quality extrusion has been increasing, and particle size of mineral filler used for compounding is getting smaller. When these small particle gets aerated, their bulk density becomes small, and conveying efficiency in the extruder dramatically decreases.
We have developed a deaeration side-feeder that will give you a solution to this problem.
See details (PDF)
Back to Top
2. Mixing screw
In plastics compounding by twin screw extruders, kneading discs or rotor elements are generally used for mixing section of the screws depending on the material and the application.
Now, JSW has developed “Twist Kneading Disc (TKD)” so as to combine the strong points of both kneading blocks and rotor elements, which enables more energy-saving mixing than conventional kneading discs.
See details (PDF)
BMS (Backward Mixing Single flight screw) has the potential to improve the quality of sophisicated material compounding, to expand the variety of products, to increase capacity and etc.
Especially, BMS has the advantage in the field of compounding with glass fiber, oil, liquid fire tetardant and etc.
See details (PDF)
Back to Top
3. Dispersion
Recently, masterbatch which contains carbon black powders with high concentration and good dispersion are preferably used in many compounding processes.
We introduce here the study for dilution of carbon black masterbatch, which is a part of our compounding technology. A great variety of screw configurations are available now and we are ready to propose you the best one suitable for your material and process.
See details (PDF)
Kneading is performed in the clearance between cylinder inside and top of screw, what is called "Tip clearance". Compounding quality level can be increased by improving the structure of tip clearance.
We took notice of cylinder structure that is another constituent of tip clearance and developed the special kneading cylinder "NIC" with a unique channel structure on cylinder inside. Here, we introduce the detailed information of NIC.
See details (PDF)
The compounding quality is depending on the dispersion status and molecular size of a secondary ingredient, the modifier, in the base polymer, and therefore, customers require the extruders of excellent dispersion performance.
The results of our tests using our Twin Screw Extruder (TEX) prove that the dispersion performance is significantly affected by the tip clearance, which consists of screw flight tip, and cylinder bore.
See details (PDF)
We have a significant number of requests from our customers for a real-time grasp of polymer behavior inside extruders during operation.
We report here our latest flow visualization method for analysis of polymer behavior inside twin screw extruder TEX. The special cylinder with sight glass window enables us to directly observe the dynamic mixing condition during extrusion.
See details (PDF)
Back to Top
4. Metallurgy
Cooming soon
Back to Top
5. Screw shaft
Cooming soon
Back to Top
6. Material feeding
When powder materials are fed into an extrusion process, the capacity of extruder depends on the properties of powder.
We introduce here a special compactor developed by JSW to effectively remove gases from powder material to prevent such feed-neck and ensure stable feed of fine powder.
See details (PDF)
Back to Top
7. Gear box
Cooming soon
Back to Top
8. Screening
Cooming soon
Back to Top
9. Die plate
Cooming soon
Back to Top
10. Pelletizing
Cooming soon
Back to Top